Understanding the Low Pressure Casting Process
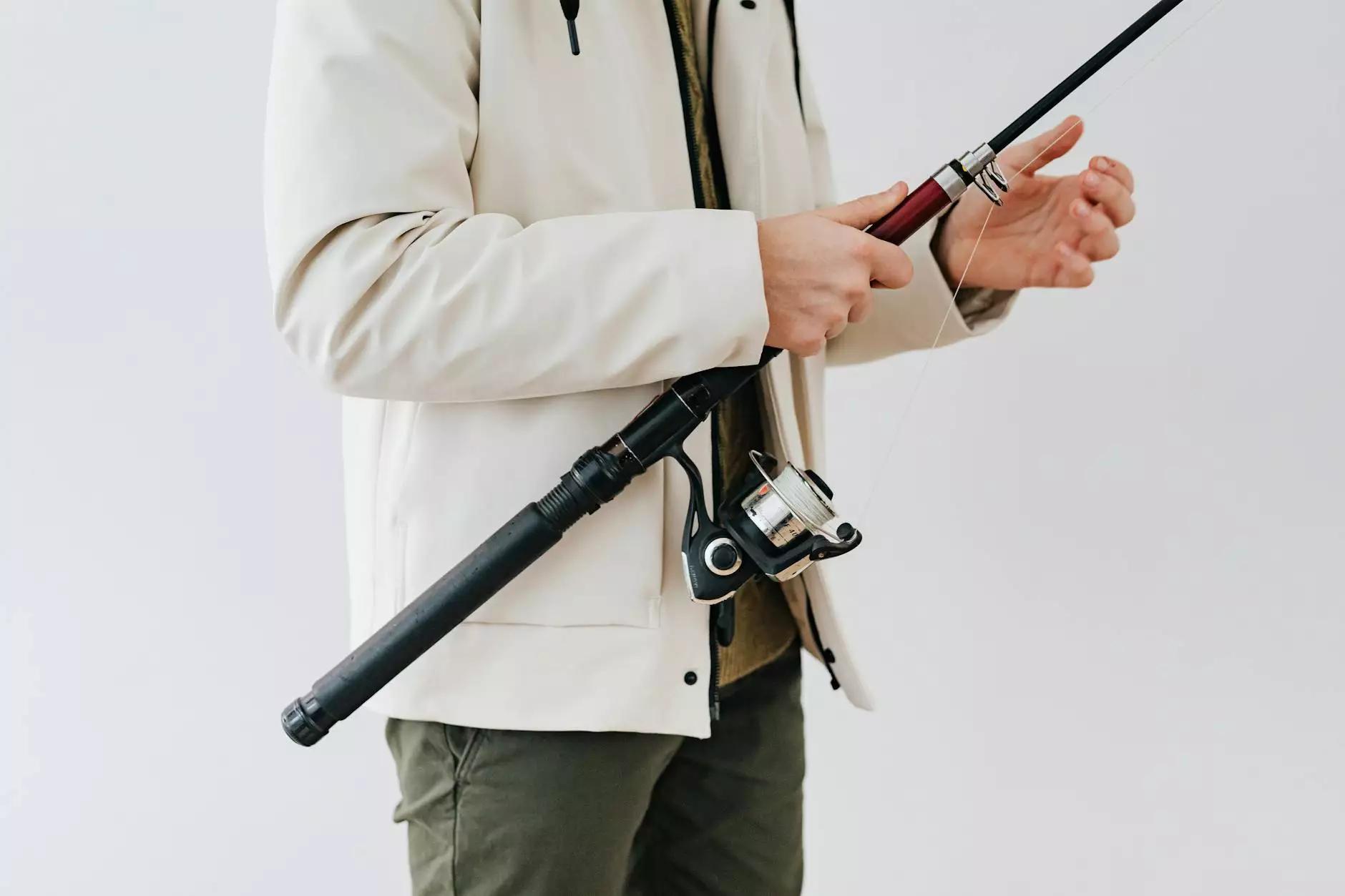
The low pressure casting process is an innovative metal casting technique that has gained significant attention in various industries, including art supplies, product design, and 3D printing. This article delves into the intricacies of this remarkable process, detailing its advantages, applications, and the technologies that make it an ideal choice for manufacturers looking for precision and efficiency.
What is Low Pressure Casting?
The low pressure casting process involves the use of controlled gas pressure to force molten metal into a mold. This method offers several advantages over traditional gravity casting and high-pressure methods, making it a preferred choice for producing complex shapes and high-quality finishes.
How Does the Low Pressure Casting Process Work?
Understanding the workings of the low pressure casting process is essential for grasping its advantages:
- Preparation of the Mold: Molds are typically manufactured from metals or high-grade refractory materials to withstand high temperatures.
- Melting Metal: The desired metal, often aluminum or zinc alloys, is melted in a furnace.
- Mold Insertion: Once the metal reaches the appropriate temperature, the mold is positioned vertically.
- Pressurizing the Gas: In this step, a low gas pressure (usually between 0.5 to 2 bar) is applied to push the molten metal into the mold cavity.
- Cooling and Solidification: The molten metal cools and solidifies within the mold.
- Demolding: Finally, the cast component is removed, showcasing its precise dimensions and finely finished surface.
Benefits of Low Pressure Casting
The low pressure casting process offers numerous benefits, making it a preferred method in various sectors:
1. Enhanced Product Quality
One of the notable benefits of low pressure casting is the improved quality of the final product. The controlled environment during the casting process minimizes defects such as porosity, ensuring that the end products are robust and durable.
2. Efficient Use of Materials
Low pressure casting allows for a more efficient use of materials. Since the process creates less waste compared to traditional methods, manufacturers can achieve a higher yield while minimizing costs.
3. Versatility in Design
This casting method supports intricate designs and complex geometries, enabling creators to innovate without limitations. The versatility inherent in this process allows designers and artists to explore new concepts.
4. Reduced Production Time
Thanks to the accelerated cooling rates and efficient molding processes, low pressure casting significantly reduces the time required for production. This advantage is particularly critical in industries where time-to-market is a competitive factor.
5. Environmentally Friendly
Low pressure casting is considered more environmentally friendly compared to traditional casting methods. The reduced energy consumption and minimized waste production contribute to a lower carbon footprint, aligning with modern sustainability goals.
Applications of Low Pressure Casting
The applications of the low pressure casting process are vast and varied, impacting several industries profoundly:
1. Product Design
In product design, low pressure casting is utilized to create prototypes, mock-ups, and final products. Designers rely on this method to achieve high fidelity in their designs, which is crucial for both aesthetics and functionality.
2. Automotive Industry
The automotive sector benefits significantly from low pressure casting when producing components such as engine blocks, transmission housings, and various structural parts. The strength and precision offered by this method ensure that parts meet rigorous performance standards.
3. Aerospace Engineering
The aerospace industry requires the highest standards of quality and performance. Low pressure casting is employed to manufacture components with exceptional strength-to-weight ratios and precise tolerances, essential for aircraft safety and efficiency.
4. Art and Sculpture
Artists use low pressure casting techniques to create sculptures and artistic installations. With the ability to replicate intricate details, this process facilitates the transformation of artistic visions into tangible works.
5. 3D Printing Technologies
As 3D printing technology continues to evolve, low pressure casting complements this field by enabling the production of metal parts that can be used as finished applications or as components in larger assemblies.
Comparing Low Pressure Casting with Other Methods
The low pressure casting process often stands in contrast to traditional casting methods, such as gravity casting and high-pressure casting. Here’s how these methods compare:
Casting MethodAdvantagesDisadvantagesLow Pressure CastingHigh precision, Low waste, Complex shapesInitial setup costsGravity CastingSimple process, Lower costLimited complexity, Higher porosityHigh Pressure Die CastingHigh output, Excellent surface finishHigher costs, More limitations on metalsTechnological Advancements in Low Pressure Casting
The low pressure casting process has seen significant advancements in technology, enhancing its capability and efficiency:
1. Automated Systems
Automation in low pressure casting has transformed production efficiency. Automated systems reduce human error and increase throughput, allowing manufacturers to meet the increasing demand for precision castings.
2. Advanced Molding Techniques
With the advent of advanced materials and techniques for mold creation, low pressure casting can achieve ever-greater levels of detail and finish quality.
3. Real-Time Monitoring
Incorporating real-time monitoring systems for temperature, pressure, and mold conditions ensures optimal performance and quality control throughout the casting process.
Challenges Facing the Low Pressure Casting Process
While the low pressure casting process offers many advantages, it is not without its challenges:
1. Equipment Costs
The initial investment in equipment for low pressure casting can be significant, potentially deterring some businesses from adopting this technology.
2. Material Limitations
While most non-ferrous metals can be cast using this method, its application for ferrous metals is limited, thus confining the range of materials that can be used.
3. Skill Requirements
Operating and maintaining low pressure casting equipment requires skilled personnel, which may pose a challenge for some organizations trying to implement this system.
Conclusion
In conclusion, the low pressure casting process has established itself as a vital technology in various industries, from art supplies to aerospace. Its ability to produce high-quality, intricate components efficiently makes it an invaluable asset in today's competitive manufacturing landscape.
For businesses looking to innovate and improve production processes, understanding and embracing the low pressure casting process could be the key to unlocking new potentials and achieving long-term success. By investing in this advanced casting technique, companies can enhance product quality, reduce waste, and expedite their time-to-market, all while supporting sustainable practices.
For more information on art supplies, product design, and the latest advancements in 3D printing, visit arti90.com.